Hollow blocks are a popular choice in construction due to their lightweight nature and excellent insulation properties. Understanding how to make them can save time and money while ensuring structural integrity in various projects. This article will guide readers through the essential steps and materials needed to create high-quality hollow blocks, making DIY construction more accessible and efficient.
Understanding Hollow Blocks
Hollow blocks, also known as concrete masonry units (CMUs), consist of concrete and aggregates that form a block with hollow cores. These cores reduce weight and improve insulation properties. Hollow blocks typically measure 16 inches in length, 8 inches in height, and 6 inches in width, although variations exist based on manufacturing.
Hollow blocks provide several advantages in construction. They offer superior thermal insulation, which helps regulate indoor temperatures. Their lighter weight eases handling and transportation, streamlining construction processes. Additionally, they boast strong structural integrity when properly installed.
The material composition of hollow blocks varies but commonly includes cement, sand, gravel, and water. Manufacturers can adjust aggregate sizes and proportions to influence the block’s final properties, allowing customization for specific applications.
For those looking for an efficient and reliable way to manufacture hollow blocks, using a Lontto hollow block machine can streamline the process. These machines ensure uniformity, durability, and faster production, making them an excellent choice for both small and large-scale projects.
Hollow blocks contribute significantly to sustainability. Their ability to incorporate recycled materials enhances eco-friendliness. Additionally, their energy-efficient qualities can lead to reduced heating and cooling costs over time.
Materials Required
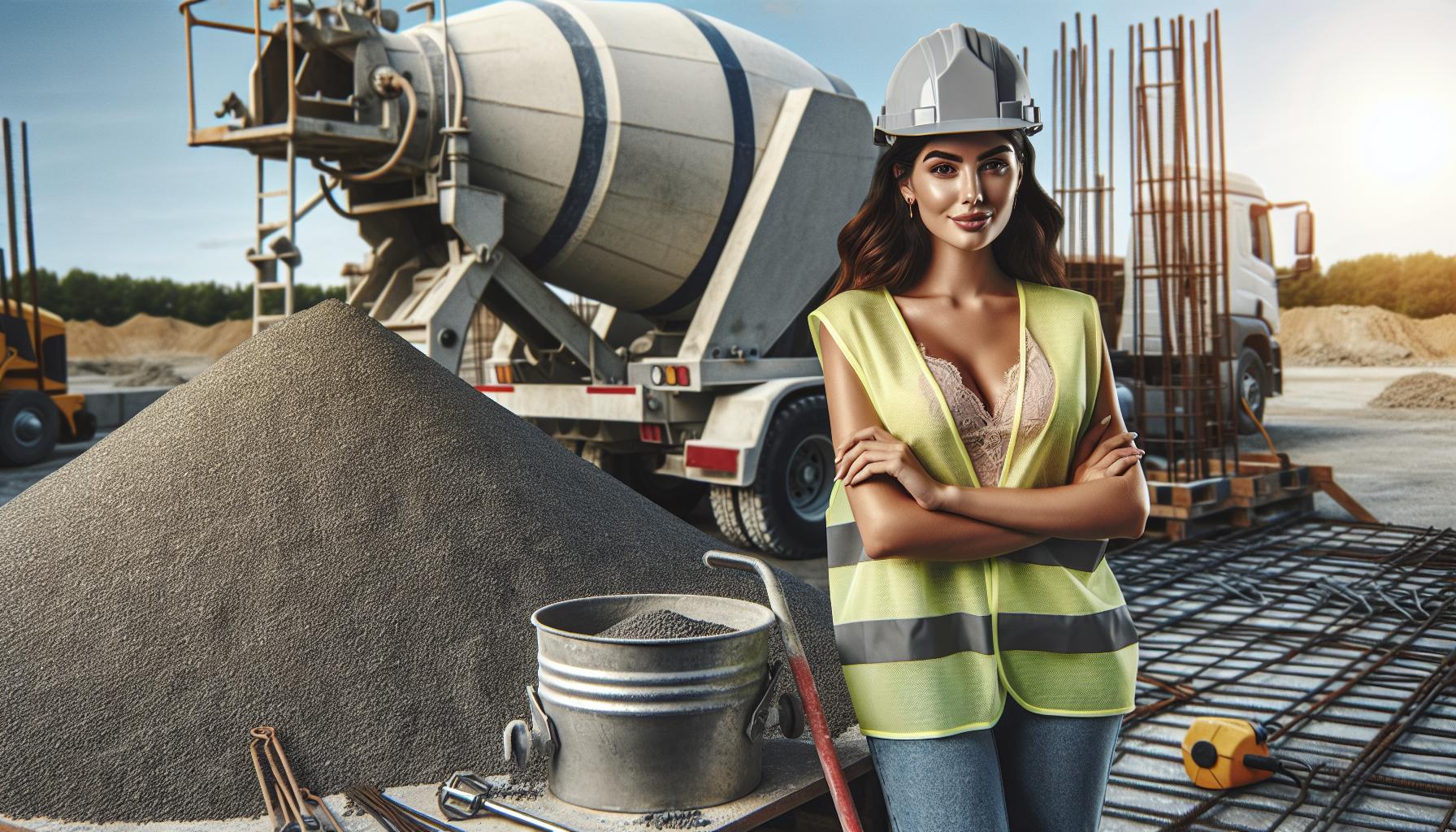
Selecting the right materials is crucial for making high-quality hollow blocks. The primary components and tools contribute to the block’s performance and durability.
Essential Ingredients
- Cement: Use Portland cement for optimal strength and setting time.
- Aggregates: Incorporate coarse aggregates, such as gravel or crushed stone, and fine aggregates like sand. The right mix enhances the block’s structural integrity.
- Water: Clean, potable water ensures proper hydration of cement and prevents contamination.
- Admixtures: Consider admixtures to improve workability, strength, or setting time, depending on project requirements.
Tools and Equipment
- Concrete Mixer: A heavy-duty mixer provides consistent mixing of ingredients.
- Molds: Utilize steel or plastic molds to shape the blocks accurately.
- Shovels: Use shovels for mixing and transferring materials.
- Leveling Tools: Include a trowel and level to ensure even surfaces.
- Compactor: A mechanical or manual compactor helps compress the mix for density.
Having these materials and tools ready streamlines the process of making hollow blocks, ensuring effective construction practices.
Step-by-Step Process
Follow these essential steps to create hollow blocks efficiently and effectively.
Mixing the Ingredients
Mixing involves combining the correct proportions of Portland cement, coarse aggregates, fine aggregates, and clean water. Use a concrete mixer to ensure uniformity. The typical ratio is 1 part cement, 2 parts fine aggregates, and 3 parts coarse aggregates. Water should be added gradually until achieving a workable consistency. Optional admixtures can improve properties such as strength and setting time.
Molding the Blocks
Molding requires using specific molds designed for hollow blocks. Place the mixed ingredients into the molds, filling them sufficiently to form a solid structure. Use a leveling tool to ensure the top surface is even. Vibrate the molds to remove air bubbles and improve density. Allow the mixture to settle into shape, ensuring that the hollow cores are correctly formed.
Curing the Blocks
Curing ensures the blocks gain strength and durability. After molding, keep the blocks moist for at least 7 days. This process maintains the necessary hydration for cement hydration. Cover the blocks with wet burlap or plastic sheets to prevent evaporation. Regularly check the moisture levels to ensure optimal curing conditions.
Common Mistakes to Avoid
- Incorrect Mixing Ratios
Many individuals mix materials inaccurately. Following the recommended ratio of 1 part cement, 2 parts fine aggregates, and 3 parts coarse aggregates ensures consistency and durability.
- Insufficient Vibration
Failing to vibrate the mixture properly can lead to air pockets within the blocks. Utilize a vibratory compactor to eliminate air bubbles and ensure even distribution of materials.
- Skipping Curing Process
Neglecting to cure the blocks can compromise their strength. Keep the blocks moist for at least 7 days, using wet burlap or plastic sheets to prevent evaporation, which enhances durability.
- Using Poor-Quality Materials
Choosing inferior quality aggregates or cement affects the overall integrity of the blocks. Always opt for high-quality materials to ensure strong and reliable hollow blocks.
- Ignoring Mold Quality
Utilizing damaged or poorly made molds often results in uneven block shapes. Invest in sturdy molds designed for making hollow blocks to achieve accurate dimensions.
- Not Allowing for Settling Time
Rushing the removal of blocks from molds can lead to deformation. Allow the blocks to settle properly before detaching them to maintain their intended shape.
- Overloading During Transportation
Transporting blocks without proper support can cause cracking. Handle blocks with care, avoiding heavy stacking or bouncing during transit.
- Neglecting Site Preparation
Poor site preparation can affect the installation and longevity of hollow blocks. Ensure a stable, level foundation free from debris before laying blocks to achieve optimal performance.
Tips for Success
- Select the Right Materials: Use high-quality Portland cement, clean coarse aggregates, clean fine aggregates, and clean water. Quality affects durability and insulation.
- Measure Accurately: Adhere to the mixing ratio of 1 part cement, 2 parts fine aggregates, and 3 parts coarse aggregates. Precision in measurement ensures consistent strength.
- Mix Thoroughly: Utilize a concrete mixer for uniform consistency. Proper mixing prevents weak spots and enhances structural integrity.
- Fill Molds Properly: Ensure even filling of molds to create uniform blocks. Poor filling can lead to inconsistent sizes and strength issues.
- Vibrate Efficiently: Apply adequate vibration to eliminate air bubbles. Air pockets weaken the blocks, reducing compressive strength.
- Cure for Optimal Strength: Maintain moisture for at least 7 days during curing. Use wet burlap or plastic sheets to retain moisture and promote hydration.
- Prioritize Site Preparation: Level and compact the ground where the blocks will cure. A stable setup helps prevent settling and cracking.
- Inspect Molds Regularly: Check for wear and tear. Damaged molds can produce misshapen blocks, impacting overall quality.
- Transport with Care: Avoid overloading during transport to minimize damage. Handle blocks carefully to prevent breakage.
- Keep Records: Document mixing ratios, batch numbers, and curing times. Logging this information aids in quality control over time.
Conclusion
Mastering the art of making hollow blocks opens up a world of possibilities for construction projects. With their lightweight design and excellent insulation properties, these blocks not only improve structural integrity but also contribute to sustainability. By following the outlined steps and avoiding common pitfalls, anyone can produce high-quality hollow blocks that meet specific needs.
Investing time in the right materials and methods ensures durability and efficiency in any building endeavor. As DIY construction becomes more accessible, the knowledge gained from this process empowers individuals to take control of their projects while achieving professional results. Embracing these techniques can lead to significant savings and a more sustainable approach to building.
Frequently Asked Questions
What are hollow blocks and their benefits in construction?
Hollow blocks, or concrete masonry units (CMUs), are lightweight blocks with hollow cores, improving insulation and reducing weight. They also offer strong structural integrity and energy efficiency, leading to lower heating and cooling costs. These advantages make them a popular choice for sustainable construction projects.
How do you make hollow blocks?
To make hollow blocks, mix 1 part Portland cement, 2 parts fine aggregates, and 3 parts coarse aggregates using a concrete mixer. Fill molds evenly and vibrate to remove air bubbles. Cure the blocks for at least 7 days to ensure strength and durability.
What materials do I need to create hollow blocks?
You will need Portland cement, coarse and fine aggregates, clean water, and optional admixtures for performance enhancement. High-quality materials are crucial for making strong and reliable hollow blocks.
What tools are essential for making hollow blocks?
Essential tools include a concrete mixer, molds, shovels, leveling tools, and a compactor. These tools streamline the process and ensure effective construction practices when making hollow blocks.
What common mistakes should I avoid when making hollow blocks?
Avoid incorrect mixing ratios, insufficient vibration, skipping the curing process, using poor-quality materials, and neglecting site preparation. Overloading during transportation and not allowing for settling time can also lead to problems.
How can I ensure the quality of my hollow blocks?
To ensure quality, select high-quality materials, measure accurately, mix thoroughly, fill molds properly, and vibrate efficiently. Regularly inspect molds, cure properly, and transport with care while keeping detailed records for quality control.